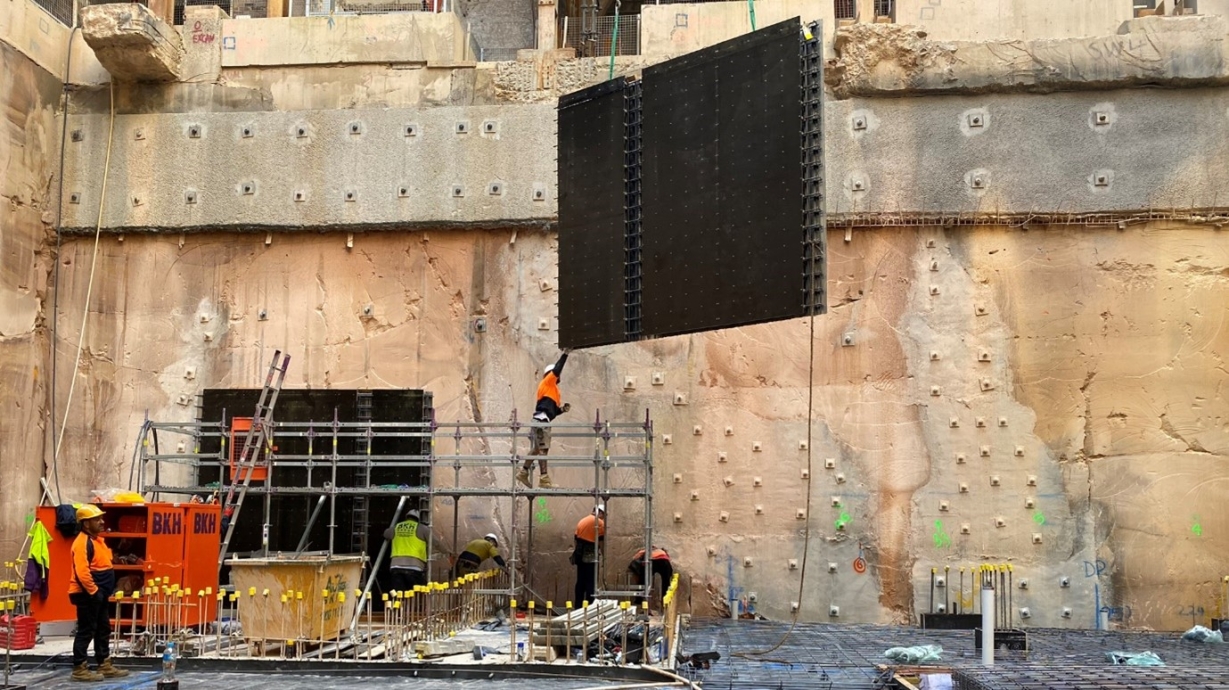
Ozwall is a unique prefabricated vertical formwork system created in Australia and applied here and overseas with great success. The clever technology was conceived and developed by structural engineer Geoff Wyett, founder and director of Ozwall, to overcome the limitations of traditional onsite approaches to vertical formwork. With the pressures on construction projects only intensifying, we spoke with Geoff to get an insight into his system, the problem it solves and the various benefits for users of the technology.
Geoff, you’ve been involved with concrete for a long time. Tell us about your background.
In the late 1980s I managed and then acquired a specialist concrete repair and waterproofing contractor. This gave me a lot of exposure to challenging and high-profile projects. This included earthquake rectification work in Guam in 1993 on a US$3M project involving 5 kilometres (kms) of crack repair and in 1996 the A$5.3M repair of the Christchurch Cathedral in Newcastle, Australia. The Christchurch Cathedral project involved drilling a total of 3.5 kms of holes and installing anchors using the Cintec anchor system. At the time, we drilled the world’s longest 32mm horizontal hole. I also did 7,500 m2 of remedial work on a major Sydney hotel. The basement would flood within 24 hours if the dewatering system shut down and the hotel was about to be closed because the lift shafts were considered unsafe.
How did these experiences lead you to create Ozwall?
It highlighted two things in me: First, the time and budget challenges of onsite work; and second, the quality issues that can arise and then need remediation. Through experience, I was very aware of the impacts of working onsite and I was proud that we were somehow able to manage the various challenges of onsite work within budget and deadline constraints. But it planted the seed in my mind that taking things offsite could minimise the inherent risks.
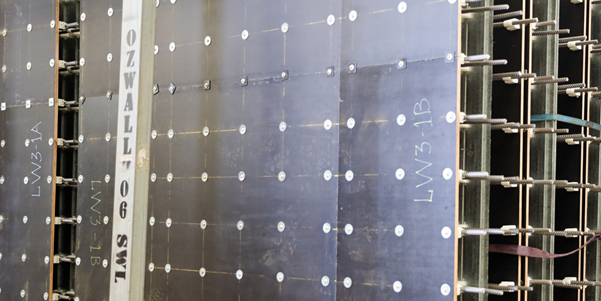
When did Ozwall get started?
Ozwall's journey began in 1997. I saw an opportunity to convert an Adelaide-based partition panel called Rapidwall into a full load-bearing wall and so I funded and directed all R&D including acoustic, fire and structural testing. The result was the world-first installation of a full load-bearing concrete-filled wall made from hollow precast glass reinforced plaster (GRP). In total, we installed 46,000m2 of wall in 371 apartments up to 10 storeys high.
I formed Ozwall in 2005 to develop my own GRP product and commenced production under a patented vertical casting system in 2006. There was a construction boom in Dubai, so I headed there in 2007 and established a manufacturing facility to service major projects including Dubai Motor City. We sold under the Gulfwall brand, producing 25,000m2 per month with demand exceeding supply.
I returned to Australia in 2010 once the boom ended and started to develop the current Ozwall vertical formwork technology.
Tell us about your current Ozwall system.
It's an offsite-manufactured alternative to the conventional method of producing vertical formwork elements entirely onsite. We offer two systems, both using the prefabricated reinforcement cage as an internal skeleton to which the formwork is attached using the Ozwall technology:
Permanent Formwork, which consists of a profiled metal sheet which is attached to the reinforcement cage using the patented Ozwall T-Clip technology. The metal sheet is sacrificial and remains in place.
Removable Formwork, which uses conventional Formply (plywood engineered specifically for concrete formwork) which is attached to the reinforcement cage using the patented Ozwall Connector and then removed after pouring the concrete for reuse.
What configurations do you typically supply?
Walls on boundaries or with difficult access would use the permanent metal sheet and T-Clip system on the outside face and the inside face would use the removable system with Formply and Ozwall connectors. Internal walls would use the removable system on both faces.
To install onsite, both sides of the element and the reinforcement cage are lifted into place as a single unit. This is very fast and reduces crane time and onsite labour requirements. Lift shaft walls would usually take a single element; however, a stair shaft wall would usually come in two parts to limit transport length. We usually create walls up to 4m long and 4m high to allow for vertical transportation for easy craning into position.

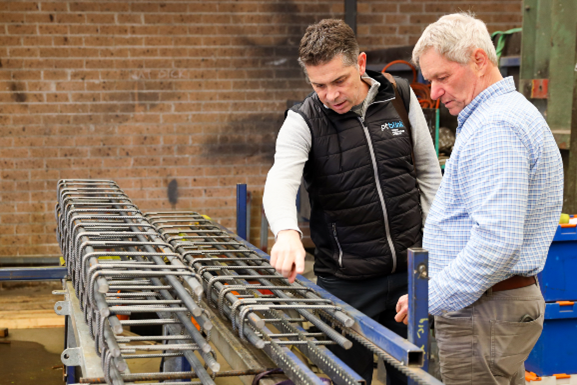
What opportunities does PT Blink’s Design – Manufacture – Integrate process open up for you?
We are currently called on mostly to solve a difficult access problem – for example, formwork required right on the boundary. The wall geometry is set. With a process like Blink DMI® and the Blink Backbone® as the geometric reference point for the building project, we can be more calculated with our dimensions and resource usage. For example, we can set wall panel dimensions that suit standard Formply sizes and our propriety permanent formwork metal sheet width. This reduces material wastage and increases repeatability for much greater labour efficiency. Because we span manufacture and onsite integration, there is opportunity to optimise the entire process if we are engaged from the design phase using an established kit of standardised parts.


What challenges are you seeing in construction currently?
In 2022 the construction industry has been hit by the effects of Covid, heavy rain, escalating prices as well as a shortage of labour. The effects of rain due to La Nina in particular has caused devastating delays to onsite progress in the last 12 months and forecasts indicate that we can expect another La Nina season over the next 6 months. Several clients have advised me that their total rain day allowance has been used up in the first 20% of the project. You can’t control the weather and rain literally shuts the site down, which affects everyone. The answer is clearly to take as much work offsite as possible and immediately remove the weather impacts. Every rainy day we continue producing in our dry factory environment.
What other benefits do you see with offsite manufacturing?
We reduce site labour for formwork by 90%. This has a range of positive effects including reducing site traffic, reducing the risk of onsite injury and reducing costs by offering workforce alternatives. Carpenters for example are in high demand due to a shortage and come at a high wage premium so – for formwork – it’s far more cost-effective to use dedicated factory-based workers rather than carpenters.
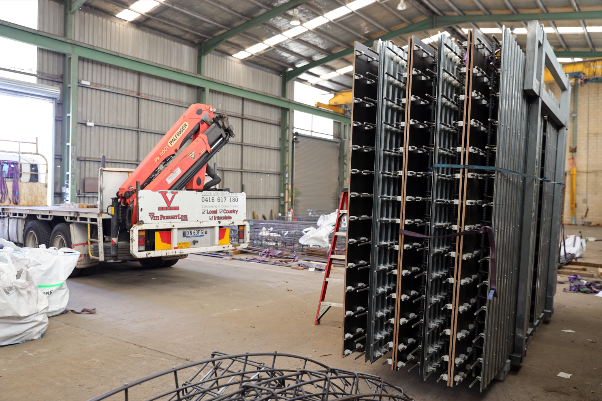
What are the benefits of being a Blink DMI™ partner?
For us, being part of a collaborative ecosystem means opportunity to realise our full potential in every sense. A coordinated system is a win for everyone from the developers and owners to the supply chain members. Being a design-led process means that you are building predictability into the project from the outset and the cloud-based platform will ensure transparency, communication and opportunity for members.
_______________________________________________
Are you a designer, manufacturer or integrator (builder)? Register your interest in becoming a Blink DMI® Partner today.