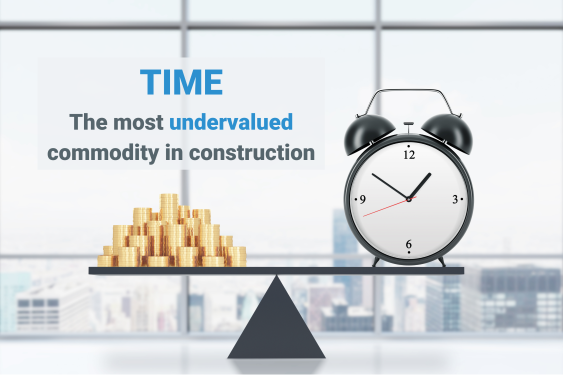
Construction inflation this year is estimated at up to 12% in some segments. According to CoreLogic, over the past 5 years, construction costs in Australia have increased more than 25%, heavily impacting builders’ margins and project budgets. Statistics from the US Census Bureau show that construction costs in the US rose 17.5% in 2021, the highest increase in 50 years and 23% higher than pre-pandemic 2019. These impacts are global, and the interconnectedness of markets sees near-universal inflationary trends in construction. At the same time, US construction projects are taking 1.5 months longer to complete, extending from 17.7 months on average in 2019 to 19.2 months in 2021.
Time is money in any industry, but it has never been more valuable than in the construction industry today. Yet, according to PT Blink Founder Murray Ellen, time is the most undervalued commodity in construction. It was this thinking that led to the genesis of PT Blink and the unique Blink DMI® method of constructing multi-storey buildings very quickly onsite from a kit of configurable, manufactured components...
Why do you say time is the most underrated commodity in construction?
Because labour productivity is simply not improving as fast as other sectors. Independent analyst reports peg global labour productivity growth in construction at an average of just 1% annually over the past 20 years, compared with 2.8% for the total world economy and 3.6% for manufacturing.
The ramifications of this low productivity across the industry, society and the economy are huge. We know there is a better way by using technology to fundamentally change the end-to-end building process rather than just trying to optimise the way things are currently done through various point solutions.
How much time does PT Blink save?
Every project is different, but we aim to save at least 40% of total project time using Blink DMI®. For example, we licenced our technology for The Fells Apartments in Spring Hill, Queensland, which used Blink DMI® for the structural backbone and a standard build for the remainder. We enabled 8 months to be shaved off the total project (reduced from 16 to 8 months), with the 7-storey backbone going up in just 11 days.
Used to full effect, our method optimises the design, manufacture and integration of all components – structural and non-structural – and that’s when we can see additional time savings.
What are the benefits of time savings?
For owners and developers, if you consider the time value of money, then we can substantially improve their internal rate of return. Shorter project time means less time paying interest, faster time to collect a return on investment and less risk exposure to things like market shifts.
General contractors have not thought much about time in the past but those with a progressive mindset are quickly realising that, with Blink DMI® potentially halving the project time, they can possibly do twice as many jobs.
For society and the economy at large, when you apply these benefits at scale, we can address a range of sustainability issues including meeting demand for social and more affordable housing. Shorter time equates to lower cost and according to the Global Economic Forum a 1% reduction in construction costs would save US $100 billion annually.
How do you save so much time?
We provide technology that enables clients to apply Blink DMI® – a cohesive method of design for offsite construction and onsite integration – using lean manufacturing and a horizontally integrated supply chain. Our starting point was to address the persistent challenges facing property projects. The industry is continually striving to manage risks, including time-to-market risk, budget-vs-cost risk, build-quality risk, resource-wastage risk and personal-injury risk.
We reduce these risks and offer a higher degree of certainty, transparency and predictability throughout the supply chain, all of which positively impact time and productivity. Offsite manufacture also minimises waste and improves safety. Today, 45% of projects globally are delayed due to adverse weather. The cost of delay is billions of dollars in additional expenses and lost revenue, and it’s getting worse due to climate changes that increase the frequency and intensity of adverse weather events at construction sites.
Working in controlled factory spaces of course reduces the effect of adverse weather events such as recent flooding in Australia and the US and extreme heat this year in the northern hemisphere. These events can shut down onsite activity and place additional pressure on labour shortages.
Our Blink DMI® method is design-led and is supported by time-saving tools that enhance creativity but achieve accuracy across the entire building, detecting and rectifying clashes at the design stage. Preventing rework down the track saves a huge amount of time and cost which is often hidden in traditional construction. With us, the design is right and directly instructs our manufacturing partners, and our digital twin will serve as a single source of truth and accuracy. As built is literally as designed.
Using our Blink Backbone® structural technology enables architectural freedom for any design, a precise geometric reference point and the ability to create buildings without a core for lateral stability. This removes the superstructure from the critical path and eliminates it as a roadblock. The superstructure and all other components can be created concurrently and integrated very fast using just-in-time principles with fewer trades on site. Faster, safer, better and less waste!
What makes PT Blink unique?
First is the flexibility of our technology. We can work with clients’ completed designs and literally 'Blink' their project by running the design data through our technology to tell them exactly how they can build faster.
Secondly, we possess patented structural and software technology but see our role as creating and empowering a horizontally integrated partner ecosystem of accredited designers, manufacturers and integrators. This includes creating a manufacturer marketplace that allows manufacturers to digitise their products and add them to the design catalogue and transact directly with clients. The ecosystem is open so, once accredited, anyone can participate, including clients’ existing partners.
We see ourselves as the antidote to vertical-integration construction and we are on a mission to contribute to a rebuilding of sovereign manufacturing capability. Once in the Cloud, our technology will pull together all the manufacturers on one platform, for the benefit or property owners and developers as well as supply chain partners.
Is your method restrictive?
Adaptability is one of the features or our unique technology. It can apply to virtually any architecture and is well suited to tricky developments out of reach to traditional construction because they are cost prohibitive. In some cases, Blink DMI® may be the only way for a job to be done for the budget. Our seismic stability benefits are another reason as is our ability to take advantage of air rights or build over existing assets, such as heritage properties.
How do clients work with PT Blink’s technology?
We are creating our cloud-based platform and marketplace and are also engaged by clients as technology partners while this takes place. We work with client teams running the design work and feasibility for them, we license our technology and we manually administer the Blink DMI® process though our partners.
We love a challenge and the opportunity to assess projects and surprise people by what’s possible when we Blink it!
Do you have a development project? Book a FREE initial consultation today to see how Blink DMI® can work for you.
About Murray Ellen
PT Blink Founder Murray Ellen is a global expert in post-tensioned steel technology and has conceived, designed and implemented projects in countries including Australia, China, United Kingdom, Hong Kong, Malaysia, Philippines, Thailand, Taiwan and Dubai.
Murray’s broad experience includes full technical implementation, construction and development responsibility for projects which he has delivered with excellence around the world. His innovative steel design technology and construction methodologies for large-spanned structures have received multiple awards and are unique in the global steel spectrum.
Today Murray empowers and inspires a team to build on his more-than 35-year legacy, IP portfolio and original vision to deliver the built environment FASTER, SAFER, BETTER and with LESS WASTE through technology.
Murray also currently serves as a Governor of Sydney University’s Warren Centre for Advanced Engineering and is a Fellow of the Australian Academy of Technological Sciences and Engineering.