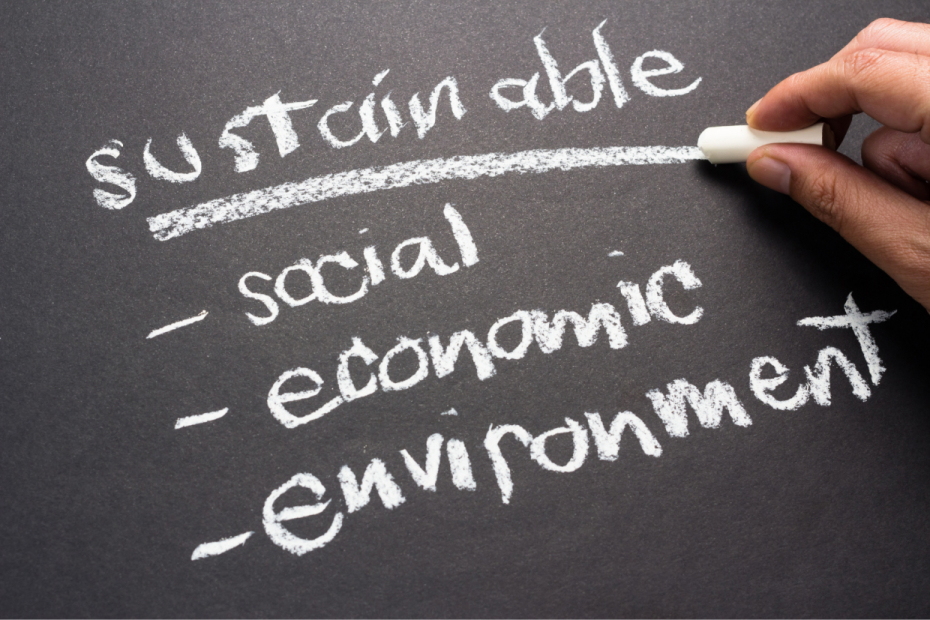
PT Blink’s philosophy is grounded in the principles of sustainability and using technology to make the world a better place tomorrow than it is today.
Mark Franklin, Executive Chairman of PT Blink, outlines some of the real impacts that the PT Blink technology platform can make across the three sustainability pillars on which it is founded.
Why is sustainability so important at PT Blink?
It is literally our reason for being. PT Blink started on the firm belief and proven understanding that, through technology and lean manufacturing principles, there is a better way to develop property.
We started with the property problem and there is a range of issues that strike at the heart of sustainability. Solving those was our goal.
What are the issues?
The construction industry is continually trying to address risks relating to delivery timeframes, cost versus budget, material wastage and worker injury. Through continuous focus and effort some companies manage these risks successfully, but when you dig into the underlying causes you see some common challenges, including:
supply chain fragmentation and uncertainty
inaccuracy and manual labour practices
too many trades on site
working out in the elements and so on.
Change has been incremental and largely focussed on optimising the prevailing way things are done. But at the heart of these risks are often decades old methodologies and fundamentally outdated technology platforms.
Mark, what are the sustainability pillars driving PT Blink’s mission?
We categorise the impacts or benefits that we enable as ‘social’, ‘economic’ and ‘environmental’. This is in line with the widely adopted framework for sustainability measurement and reporting set out by the Global Reporting Initiative standards organisation.
What makes you so passionate about the social impacts you can achieve?
If we consider the scale of the problem, we can see the importance of doing things a better way.
For example, in terms of safety there were 39 construction deaths in the UK during 2020, more than the five-year average and four times higher than the average across all industries. Falls from height, and being hit by vehicles or falling objects were the cause of death. In Australia, it was 26.
In fact, Safework Australia designates construction a ‘priority’ industry due to its high fatality rate (16% of total) and number of serious workers’ compensation claims (11%). The most common cause of injury to workers continues to be falls from height (30% in Australia) and muscular strain from carrying or lifting (16%).
This can all be dramatically improved through offsite manufacture in controlled environments with no work from height and assisted by machinery. Offsite installation of MEPF (Mechanical, Electrical, Plumbing, and Fire Protection) services also means far fewer trades onsite at any one time. Onsite integration is also highly controlled with just-in-time delivery reducing vehicles and workers onsite.
Mental health is also is major construction industry issue with twice the Australian average suicide rate and 21% of construction industry workers have a mental health issue. We address underlying causes such as the risk, uncertainty and unfair behaviour driven by financially inequitable practices of traditional construction and contract structures.
By moving to a technology-driven process like Blink DMI™, we can create a more diverse workforce and collaborative industry dynamic. Greater transparency, value creation, reward for IP and certainty are a win for all stakeholders.
Those benefits would also flow into the economy – what is the potential impact there?
Absolutely – the social factors have a huge cost impact on the economy, and great potential upside from the value-creation perspective.
The construction industry in Australia accounts for around 7% of GDP and employs more than one million people but we know there is a productivity issue. Labour productivity has remained relatively stagnant for decades globally and construction industry labour productivity has been declining annually in Australia since 2013.
According to PWC, a 1% increase in productivity would generate A$1.2 billion in savings. With Blink DMI™ aiming to achieve time savings of up to 40%, at scale we have a real opportunity to turn things around. Higher productivity will see affordable and social housing needs met and faster infrastructure development. Also improved quality and our ability to reduce operating costs will make producing affordable housing through mechanisms such as the growing build-to-rent sector much more attractive.
We also see our growing partner ecosystem and open manufacturer marketplace as a key to reigniting our local manufacturing industry and creating new jobs in the regions as we scale.
Finally Mark, what are the environmental benefits that PT Blink makes possible?
The first of these is wasted materials. In Australia every year, the construction and demolition industry generate more than 20 million tonnes of waste. Our view is that, in terms of the construction side of things, if you don’t make it you don’t waste it. Through precise, design-led offsite manufacturing, Blink DMI™ can help minimise waste in all its forms – time, money and materials.
Also, with a digital twin of the building making it possible to track parts down to the component level, decommissioning of the asset and end of life and recycling is much more precise. We will also enable clients to build to specific performance attributes such as energy consumption or embodied carbon and integrate IOT technologies such as RFID tags to measure operational performance.
Of course, this is just the beginning. When you consider the reduced impact around the building site due to distributed manufacturing and just-in-time integration, more efficient logistics and the ability to integrate more naturally with the surrounds, our environmental benefits multiply.